Fraunhofer LBF entwickelt Leichtbau-Batteriegehäuse mit integriertem Thermomanagement
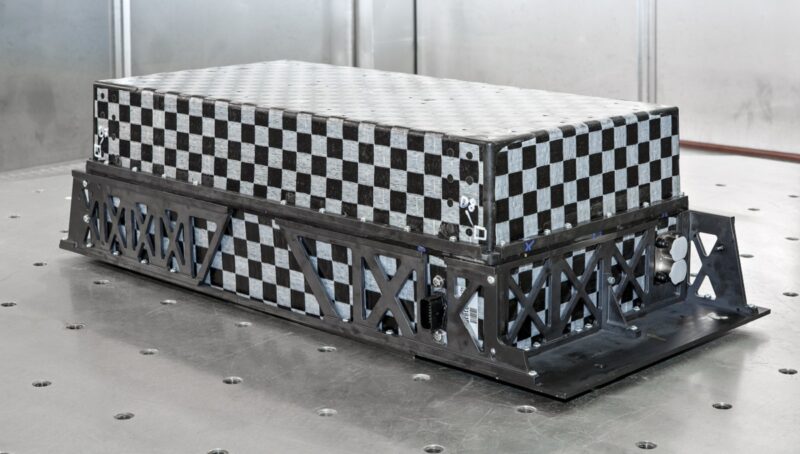
Forschende aus dem Fraunhofer LBF haben ein kosteneffizientes Leichtbau-Batteriegehäuse aus polymerbasierten Werkstoffen entwickelte. Die Gehäusestruktur besteht aus einem Polymerschaumkern und endlosfaserverstärkten Thermoplasten (CFRTP) als verstärkende Deckschichten, die mit einem neuartigen Fertigungsverfahren verbunden werden. Gegenüber herkömmlichen Aluminiumgehäusen konnten die Forscher:innen das Gewicht um 40 % senken. Zur Vorhersage des Bauteilverhaltens während der Herstellung haben sie verschiedene Simulationsmethoden entwickelt. Die Sicherheit und Zuverlässigkeit des Gehäuses für Batterie-Speicher will man anhand realitätsnaher Anforderungen im Fraunhofer LBF untersuchen.
Für Automobile gilt: Je weniger Systemgewicht, desto besser. Dank einer unermesslichen Varianz an Faserlagen, Werkstoffpaarungen und Fertigungstechnologien, ist das Konstruieren mit Faserkunststoffverbunden (FKV) die Königsdisziplin des Leichtbaus. Ein Forscherteam aus dem Fraunhofer LBF nutzte die Expertise auf diesem Gebiet ein Leichtbau-Batteriegehäuse aus Endlosfaser verstärkten Thermoplasten im dreidimensionalen (3D) Sandwichaufbau hergestellt und nutzte dazu ein neuartiges Verfahren, das den hocheffizienten Schaumspritzguss mit thermoplastischen FKV kombiniert.
In-Situ FKV-Sandwich-Verfahren für Leichtbau-Batteriegehäuse
Zum Einsatz kommt das sogenannte In-Situ FKV-Sandwich-Verfahren, welches die Herstellung fertiger Leichtbau-Batteriegehäuse innerhalb von zwei Minuten ohne Nachbearbeitung ermöglicht. Darüber hinaus lassen sich Funktionen, wie die thermische Isolationsfähigkeit oder Flammschutz, im gleichen Prozessschritt integrieren.
Die Gehäusestruktur besteht aus zwei Faserverbunddecklagen und einer verbindenden Schaumstruktur dazwischen. Die Decklagen bestehen aus unidirektionalen-Tapes, die man zunächst verwebt und anschließend konsolidiert. Das sich aus diesem Prozessschritt ergebende Laminat kann man anschließend 3D-vorformen und in ein speziell entwickeltes hybrides Schaumspritzgusswerkzeug beidseitig einlegen. Durch die gezielte Injektion eines Integralschaums zwischen die Laminate entsteht auf diese Weise die dreidimensionale Struktur des Gehäuses mit Faserverbunddecklagen und einem Schaumkern. Die Verbindung der FKV-Decklagen und des Schaumkerns, welche fundamental für die Belastbarkeit der Sandwichstruktur ist, erfolgt dabei in-situ während der Injektion.
Die beanspruchungsgerechte Sandwichkonstruktion führt zu höchsten gewichtsspezifischen mechanischen Eigenschaften und reduziert gleichzeitig den Materialeinsatz der verwendeten Faserverbund-Laminate. Die damit einhergehende Verringerung der Materialkosten bewirkt in Kombination mit den sehr kurzen Zykluszeiten des In-Situ FKV-Sandwich-Verfahrens die geringen Bauteilkosten.
23.5.2022 | Quelle: Fraunhofer LBF | solarserver.de © Solarthemen Media GmbH