Schnell, präzise, groß: Fraunhofer ISE testet neue Laser-Anlage für Wafer-Fertigung
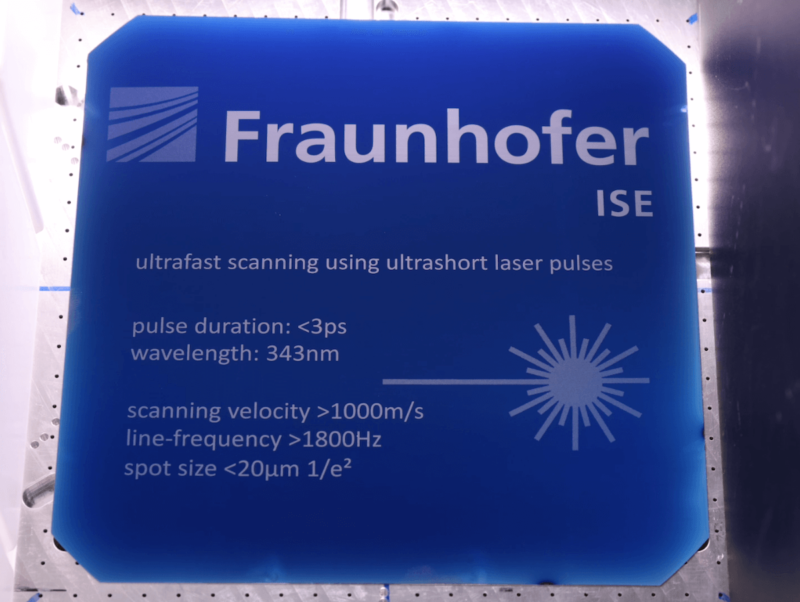
Immer größere Zellen sind quasi ein Dauertrend in der Solarbranche, um die Module immer effizienter zu machen. Schon seit einiger Zeit sind Solarzellen mit einer Kantenlänge von 210 Millimetern etabliert. Die Fertigung der dafür benötigten Wafer mit mindestens gleichbleibender Qualität und Taktrate sei für die Anlagenhersteller eine Herausforderung, heißt es in der Pressemitteilung des Fraunhofer Instituts für Solare Energiesysteme ISE. Das gelte besonders für die Laserbearbeitung.
Ein Forschungsteam des Fraunhofer ISE arbeitet daher mit Industriepartnern an einem neuen Anlagenkonzept. Es setzt auf die Kombination von „on-the-fly“ Prozessierung mit ultraschneller Scantechnologie, ultraschnellen Laserquellen, High-End Optiken und Sensorik. Im Jahr 2022 hatten die Partner die Technologie mit einem effektiven Durchsatz von über 15.000 Wafern pro Stunde demonstriert. Nun ist ein weiterer Prototyp am Fraunhofer ISE im Einsatz, der UV-Wellenlängen nutzt und daher besonders kleine Strukturen verspricht.
Laser-Anlage erfüllt drei Wünsche auf einmal
„Das Besondere am Aufbau des Demonstrators ist, dass große Werkstücke sehr schnell und mit kleiner Strukturgröße prozessiert werden können“, sagt Jale Schneider, Projektleiterin am Fraunhofer ISE. Die Laserbearbeitung soll im Idealfall drei Dinge leisten: ein großes Blickfeld, schnelle Prozessierung und feine Strukturen. „In der Branche der Lasermaterialbearbeitung ist der Gedanke fest verankert, dass man nur zwei dieser drei Eigenschaften gleichzeitig haben kann. Mit dieser Anlage haben wir alle drei Wünsche gleichzeitig erfüllt“, sagt Scheider.
Präziser Laser ermöglicht schmalere Leiterbahnen für Solar-Wafer-Fertigung
Der Demonstrator prozessiert Wafer-Formate bis zur Größe M12 (210 mal 210 Millimeter) mit Strukturen mit weniger als 15 Mikrometern Größe. Dies ist laut Fraunhofer ISE 30 Prozent kleiner als die in aktuellen Anlagen realisierten Strukturen, sofern diese ebenfalls mit Wellenlängen im UV-Bereich arbeiten. Im Vergleich zu den noch gängigeren, basierten Systemen mit IR-Wellenlängen seien die Strukturen sogar um den Faktor drei kleiner. UV-Licht ermöglicht grundsätzlich ein präziseres Arbeiten als IR-Licht, da es kürzere Wellenlängen hat.
Wenn mit dem Laser das Material für die Kontaktöffnungen ablatiert – also abgetragen – wird, lassen sich die Leiterbahnen entsprechend schmaler gestalten. Das spart nicht nur Platz an der Zelloberfläche, sondern auch Material bei der Metallisierung.
Neuer Prototyp im Test am Fraunhofer ISE
Für den Aufbau des Prototyps baute die Moewe Optical Solutions GmbH einen ultraschnellen Polygonscanner für UV-Wellenlängen mit einer Linienfrequenz von bis zu 1800 Linien pro Sekunde. „Der Einsatz des Polygonscanners erlaubt eine 10 bis 20-fach schnellere Bearbeitung der Wafer, als es mit herkömmlichen Galvanometerscannern möglich ist“, sagt Dr. Florian Rößler von Moewe Optical Solutions.
Die EdgeWave GmbH entwickelte einen neuen UV-Laser. Er ermöglicht es, bis zu 10 Millionen Laserpulse pro Sekunde zu emittieren (10 MHz), die jeweils eine maximale Pulsenergie von 5,6 Mikrojoule haben. Zudem sollen die Pulsfolgen „komplett arbiträr“ sein, sich also genau nach Bedarf einstellen lassen. „Die Realisierung einer ,pulse on demand´ Funktion ist anspruchsvoll, aber für die wachsenden Anforderungen in der Lasermaterialbearbeitung essenziell“, sagt Dr. Keming Du von der EdgeWave GmbH.
Um das Potenzial des ultraschnellen Scanners und Lasers zu erschließen, integrierte das Fraunhofer ISE sie gemeinsam mit einer High-End Optik, einer Achse und der Strahlführung zu einem Anlagen-System. In diesem testen die Forschenden nun neue Abläufe, um den Durchsatz zu erhöhen. Damit dabei die Präzision erhalten bleibt, müssen die Komponenten jede für sich eine hohe absolute Genauigkeit haben und obendrein synchron arbeiten – bei dem hohen Tempo und den winzigen Strukturen ist das laut Fraunhofer ISE keine leichte Aufgabe.
Quelle: Fraunhofer ISE | solarserver.de © Solarthemen Media GmbH